Chrome Plating Vs. Powder Coating
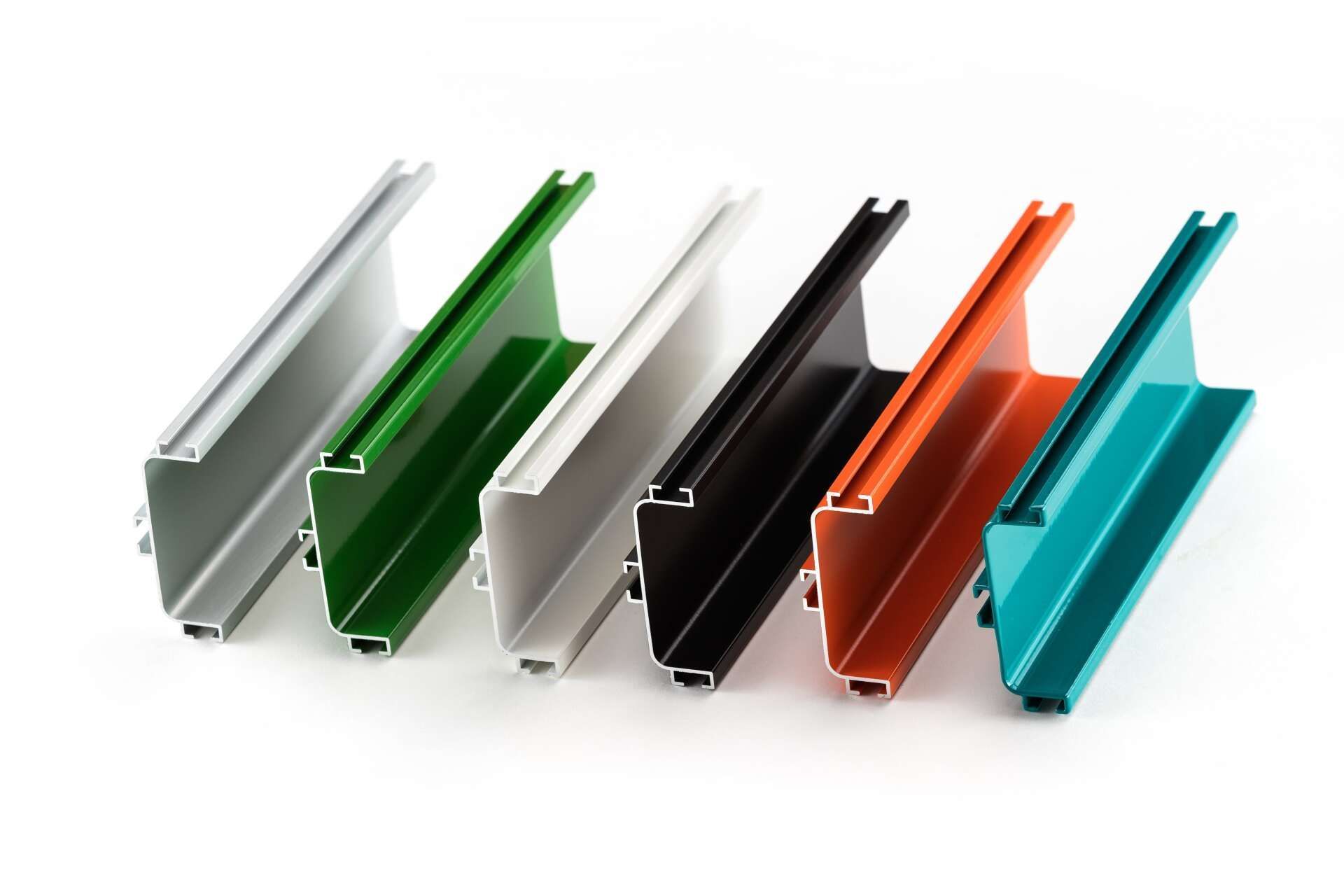
Adding a protective coating is important for many products, especially metal parts which are vulnerable to oxidation, chemicals, weather, and other destructive elements. Two common approaches, chrome plating and powder coating, are both effective in many cases, but most of the time, powder coating is a better choice.
What Is Powder Coating?
The powder coating process involves the application of a powdered plastic resin through a fluidized bed or with a spray gun that relies on electrostatic charges to permanently adhere the coating to a surface. The coated part is then heat cured to finish the process.
What Is Chrome Plating?
Chrome plating also involves an electrostatic charge, but instead of a plastic powder, parts are immersed in a liquid chromium solution.
Comparing Powder Coating and Chrome Plating
Multiple factors can influence your choice between these coating options, including:
Durability
Powder coating provides an exceptionally durable coating for countless surfaces, due in large part to the electrostatic nature of the bond between the plastic resin and the surface being coated. So many different plastic resins are available, and each offers different resistance to UV light, chemicals, corrosives, weather, abrasion, and other hazards.

Chrome coating is long-lasting, especially when applied in a thicker coat, as is more commonly used in industrial situations. Thinner coats in particular can be prone to brittleness and cracking, and if not well polished, can retain water causing lime scale. It is not suitable for flexible surfaces, and in most cases is less durable than powder coating.
Cost
Powder coating is almost always less expensive than chrome plating. In addition, chrome plating often requires multiple applications to create a coating of the desired thickness, increasing the overall coating cost.
Thickness
Each method allows multiple coats and techniques to create a coating of the desired thickness, though chrome plating is usually quite a bit thinner than powder coating.
- Chrome plating is typically .005 to .05 mils.
- Spray powder coating is typically 1 to 4 mils.
- Fluidized bed powder coating is typically 10 to 15 mils.
Appearance
Chrome plating will typically be the familiar, shiny, silver color, though some additives can produce a darker chrome and additional treatments can supply other colors and finishes.

Powder coating can be achieved in virtually any color and with a variety of finishes.
Environmental Concerns
Chrome plating typically uses lead anodes plus, of course, chromium, both of which are toxic heavy metals.
Powder coating is far more environmentally friendly, requiring no solvents, volatile organic compounds (VOCs) or other toxic materials, and is a naturally low-waste process.
At Precision Dip Coating, we offer powder coating and related services to help make your product the best it can be. Contact us today to take advantage of our decades of plastic coating and molding expertise.