Coating Services for the electrical industry
Insulation Equals Safety
At Precision Dip Coating, we specialize in providing superior metal finishing and plastic coatings for a broad range of industries. Our expertly applied coatings enhance the durability, functionality, and aesthetic appeal of metal and plastic components, ensuring they meet the highest standards of quality and performance. Leveraging advanced technology and years of experience, our team delivers customized solutions tailored to each client's specific needs. Discover how our metal finishing and plastic coating services can elevate the value and longevity of your products.
Electrical Coating Options
From powering our devices to illuminating our skyscrapers, we are dependent on electricity. It is important to protect these power sources from damage and to prevent serious incidents such as static, fire and electrocution. At Precision Dip Coating, we provide electrical protection coatings for many industries including the following:
Common Uses of Electrical and Bus Bar Plastic Coatings
Our electrical coating services are commonly used for:
Our electrical coatings include:
The Electrical and Bus Bar Plastic Coating Application Process
Coatings are applied via liquid vinyl dip coating for very thick film applications (.040”-.250”) and fluid bed powder dip coating or thick film powder coatings (.010”-.040”).
Our electrical coatings adhere to (but are not limited to) the following industry specifications: 
Contact Us Today!
At Precision Dip Coating, we specialize in protecting and insulating all components of electrical applications. If you have any questions about the products we coat or the specifics of our process, please give us a call. Our team is dedicated to providing you with the information and support you need to make informed decisions about your coating requirements.
Contact Us
Contact Us
Related Services
For more information about our manufacturing services, call us at 203-805-4564 or visit our contact page.
Why Choose Us
Wondering why Precision Dip Coating should be your top choice for dip coating and molding services? Here's what sets us apart:
Industry Experience
Decades of Professional Expertise
Value-Added Services & Support
Beyond Service, Added Value Support
Integrated Design & Development
Expertise From Concept To Completion
From Prototype to Production
Turning Ideas Into Reality, Refining Craftsmanship
Frequently Asked Questions
What is electrical and bus bar plastic coating?
One of the main functions of electrical and bus bar plastic coating is to protect the metal surface from corrosion. The coating forms a barrier between the metal and the environment, preventing contact with moisture, oxygen and other elements that can cause rusting. Additionally, a coat of plastic can help improve the appearance and durability of the metal surface.
What type of products can benefit from metal finish plastic coatings?
Metal finish plastic coatings can be applied to a variety of products to improve their appearance and performance. Some of the most common applications include automotive parts, appliances, and packaging. The coatings can help protect the metal from corrosion, scratches, and other damage. They can also make the surface more resistant to stains and dirt buildup.
How long does electrical and bus bar plastic coating last?
The life of the electrical and bus bar plastic coating largely depends on the environment in which it is used. If the environment is relatively clean and dry, the coating can last for many years. However, if the environment is dirty or wet, the coating may not last very long. In general, most coatings will last for at least five years, but they may need to be replaced more frequently in dirty or wet environments.
Why is plastic coating so effective for electrical applications?
Natural characteristics of most plastic resins make them ideal solutions for the electrical industry, including:
- Excellent insulation capabilities (high dielectric strength, low conductivity)
- Resistance to moisture, chemicals, corrosion, and oxidation
- High performance in extreme conditions
- Barrier against dust, debris, environmental contacts
- Resistance to impacts, abrasions, and other physical damage
Are plastic coatings suitable for high-voltage applications?
Yes, plastic coatings offer the combination of insulation and protection high-voltage equipment and tools need to have to maintain safety and work smoothly.
Which powder coatings are best for bus bars?
Which are the most common coatings for the electrical industry?
Plastisol is a popular dip coating for electrical equipment and tools used in electrical work, standing up to the challenges of protection in harsh environments. Epoxy, vinyl, polyolefin, Halar™ and nylon are also commonly used for electrical applications, applied by fluidized bed or electrostatic spray.
How do plastic coatings improve safety for the electrical industry?
At the simplest level, plastic coatings keep electricity where it should be, and protect people, animals, other components, and objects from coming into contact with electrical current. Plastisol coatings on tools offer additional protection to workers, especially when working in hazardous weather conditions.
Our Blog
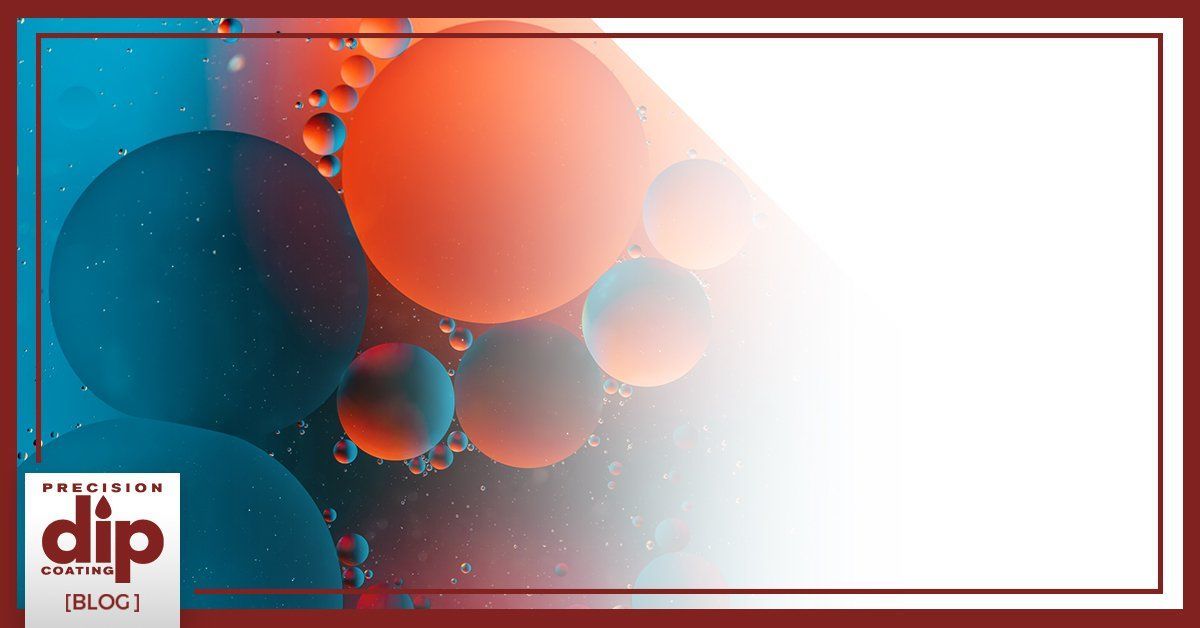
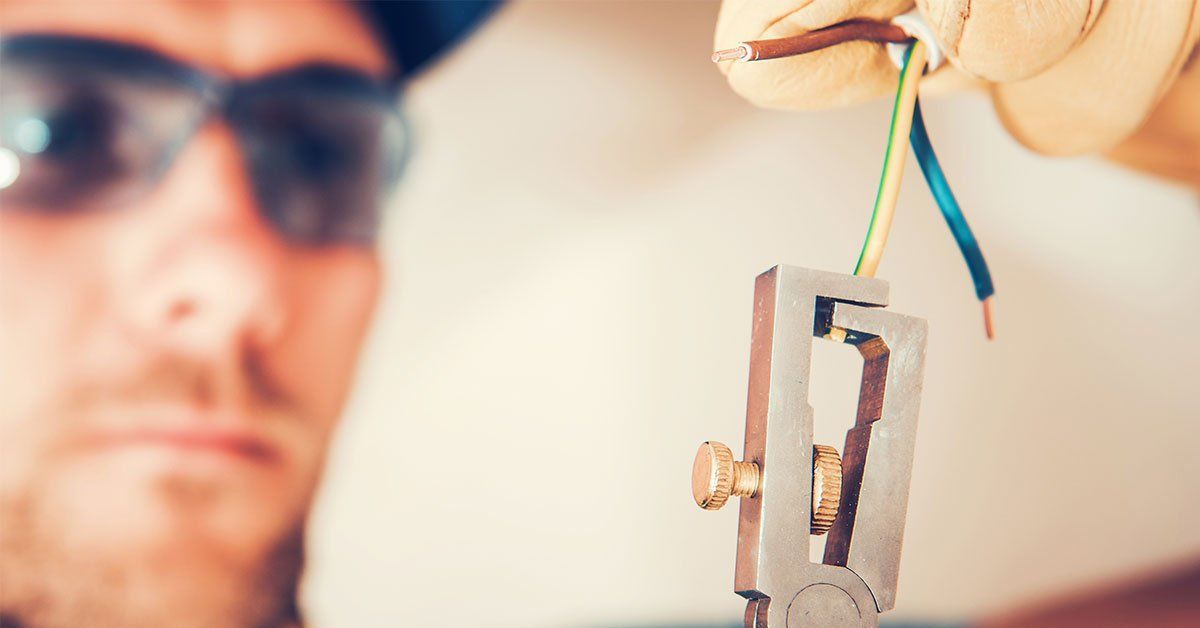