Why Bus Bar Coatings Matter
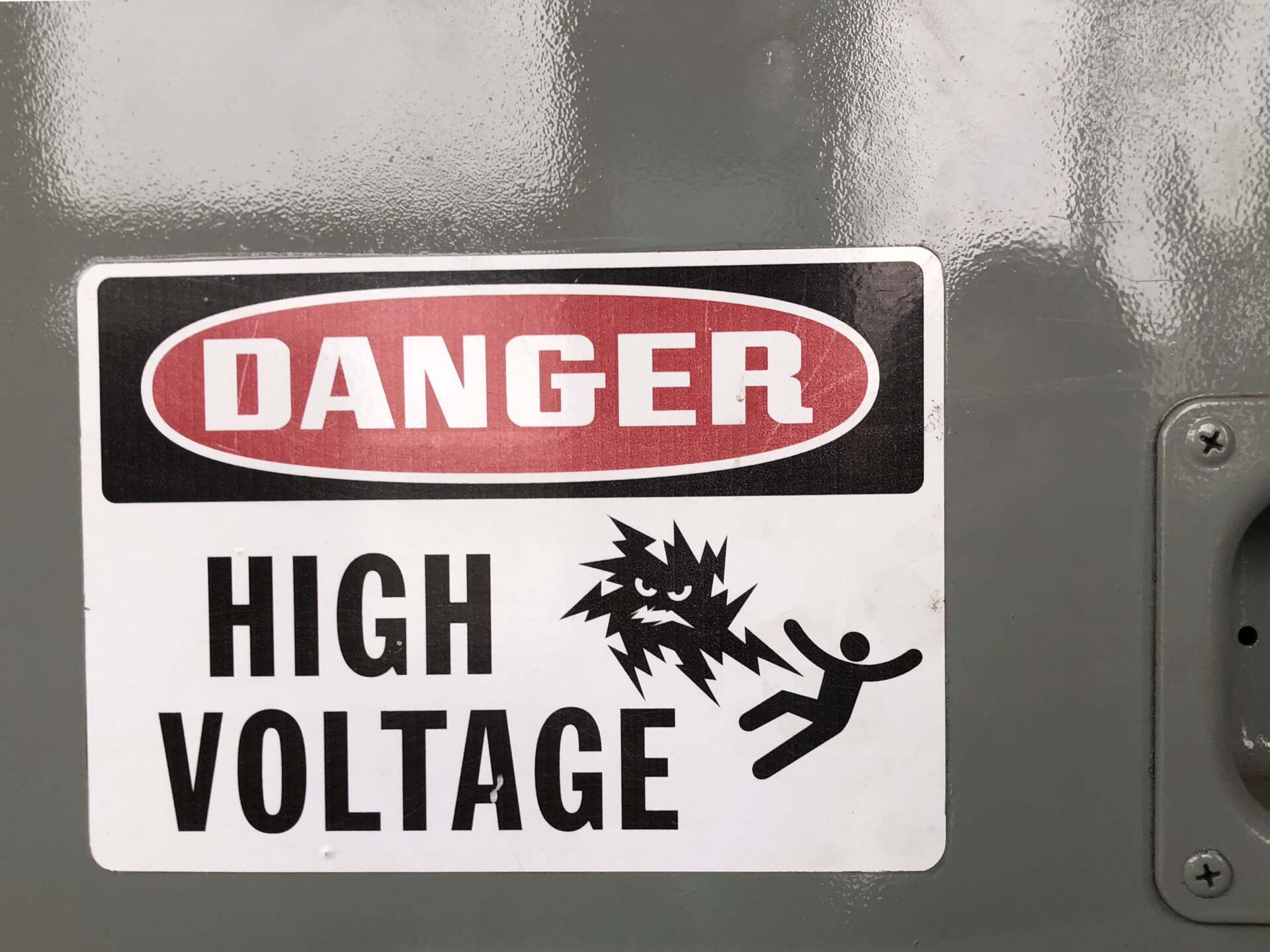
If you use electricity, you're taking advantage of the important job bus bars play in transmitting it throughout generation and distribution systems. From cell phones to power stations and everywhere in between, bus bars help electricity travel safely and efficiently to where it's needed.
What Are Bus Bars?
Bus bars, or busbars, are metal strips or rods, typically made of copper, brass, or aluminum, that connect parts of electrical distribution systems. While small bus bars are used in a variety of electronics, larger bus bars are a vital component of both low- and high-voltage environments, including power generation applications, aluminum smelters, electric vehicles, electrical service panels, switchyards, generators, charging stations, and battery banks. Systems of bus bars are commonly used to supply power in facilities such as factories and hospitals.
Why Do Bus Bars Need Coatings?
Efficient conduction is a vital part of any electrical system, and coating bus bars can help maintain them at their peak ability to conduct current. Many powder and dip coatings are suitable for electrical applications, although epoxy, vinyl, and plastisol are most commonly used to protect bus bars from corrosion, oxidation, and electrical hazards.
How Do Coatings Protect Bus Bars from Corrosion and Oxidation?
Corrosion and oxidation can reduce the ability of a bus bar to efficiently do its job by increasing resistance and even contributing to possible overheating and system failure. Powder coating on bus bars protects them from exposure to air, moisture, and other contaminants that contribute to oxidation and corrosion. By sealing the metal surface, coatings extend the lifespan of the bus bars and ensure consistent electrical performance.
How Do Coatings Improve Bus Bar Safety?
Bus bars, particularly in high-voltage environments, carry substantial electrical loads. Without proper insulation, they pose serious safety risks, including electrical shock, short circuits, and arc flash incidents. Coatings such as plastisol provide a protective insulating layer that reduces the risk of accidental contact, making systems safer for workers. Additionally, coated bus bars minimize the buildup of dust and debris, which can contribute to electrical faults over time.
What Are the Best Coatings for Bus Bars?
Choosing the right coating depends on the specific application and environment in which the bus bar is used. The most commonly used coatings include:
Do Coatings Affect Electrical Conductivity?
A common concern is whether coatings reduce a bus bar’s ability to conduct electricity. While coatings do add a protective layer, they are typically applied in a way that preserves electrical conductivity where needed. Selective coating techniques ensure that only non-contact areas are coated, leaving connection points exposed to maintain optimal electrical flow. Some coatings are even formulated to enhance conductivity while still offering protection from environmental damage.
Bus Bar Coatings With Precision Dip Coating
At Precision Dip Coating, bus bar coatings are just one of the many ways we serve the electrical industry. Our insulating, dielectric coating services protect your electrical components and improve workplace safety. With expertise in epoxy, vinyl, and plastisol coatings, we ensure your bus bars are shielded from corrosion, oxidation, and electrical hazards. Contact us today to learn more about our bus bar coatings!