Tried and True Methods for Effective Plastisol Coating
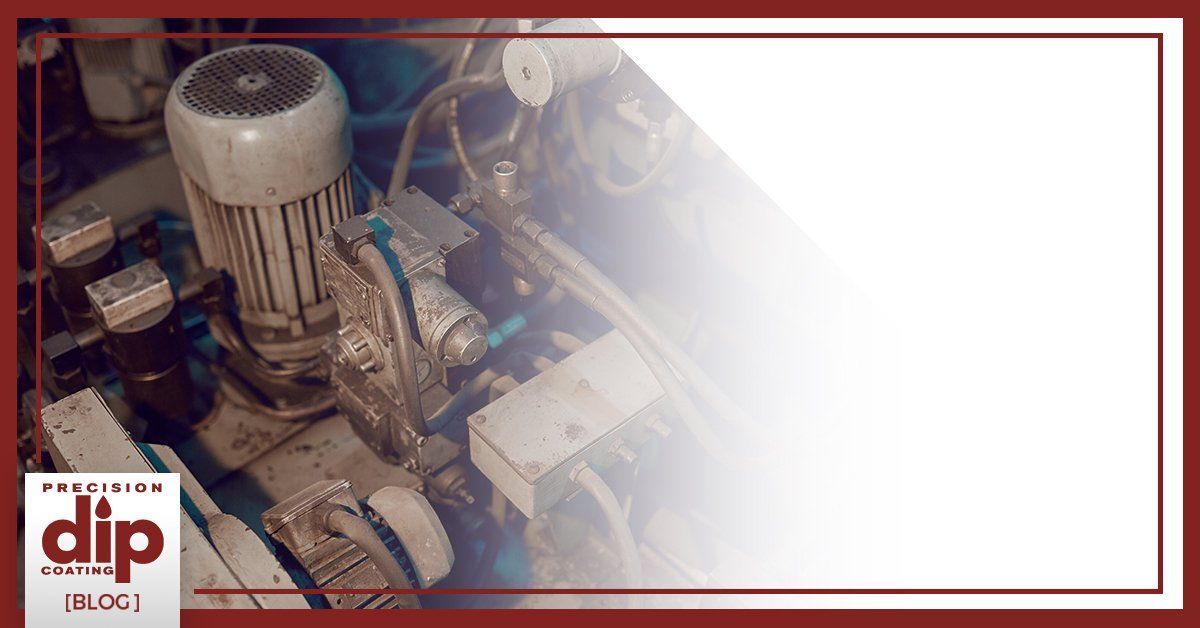
Plastisol is a versatile, highly resistant, durable, flexible coating suitable for an exceptionally wide range of uses and applications. A blend of polyvinyl chloride (PVC) or similar polymer particles with a plasticizer (a substance that makes compounds stretchier and more flexible), plastisol performs best when suitable coating methods are used.
Why Is Plastisol So Useful?
Plastisol offers many valuable benefits as a plastic coating, including:
Softness and Better Grip
Plastisol has a smooth, flexible feel that makes tools easy and comfortable to hold. Think of the handle of a favorite screwdriver or pair of pliers -- that rubbery coating is probably plastisol.
Chemical & Moisture Resistance
Resistant to acids, alkalines, and many other chemicals and corrosives, plastisols can perform well in a variety of conditions and exposures, protecting against moisture exposure at the same time.
Electrical Resistance
Combining excellent dielectric strength with great flexibility, plastisol is perfect for coating and sheathing wires and other electrical components.
Cold Tolerance
Plastisol retains its strength and feel at temperatures as low as -65°F, making it suitable for many outdoor uses.
Long-Lasting
Durable and impact-resistant, plastisol can protect from impacts and abrasions without chipping or fraying.
Best Techniques with Plastisol
Plastisol is most commonly applied as a dip coating, but can also be applied as a spray coating or in several molding processes.
Plastisol Dip Coating
Items to be dip coated (substrates) are either preheated (hot-dip) or not (cold-dip) then submerged partially or fully in the liquid plastisol. Coats of varying thicknesses can be achieved by adjusting the temperature of the substrate -- the hotter the temperature, the thicker the coating. Items are then heated at least briefly to cure or solidify the plastisol coating, then allowed to cool.
Plastisol Spray Coating
Spray coating with plastisol adds a thin layer of plastisol to the substrate. After spraying, the coated substrate must be heated to cure or solidify the coating, then allowed to cool.
Plastisol Molding
Additional techniques can be combined with dip coating to ensure thorough coats on items with more complicated shapes such as crevices, hollows, and cavities. Slush molding involves placing dipped items into a spinning centrifuge which forces the liquid plastisol to spread throughout a part. Rotational molding slowly turns a hollow part so that the interior is fully coated with the liquid plastisol. In both molding cases, the coated product must be heated to cure the plastisol.
Versatile plastisol and its array of application techniques make it a durable, valuable coating for protective, functional, and safety uses. At Precision Dip Coating, we have decades of experience and expertise with plastisol and other plastic coatings.
Contact us today to see how our plastisol and other coatings can improve your products.