Electrostatic vs Fluid Bed Coating - Which is Right for You?
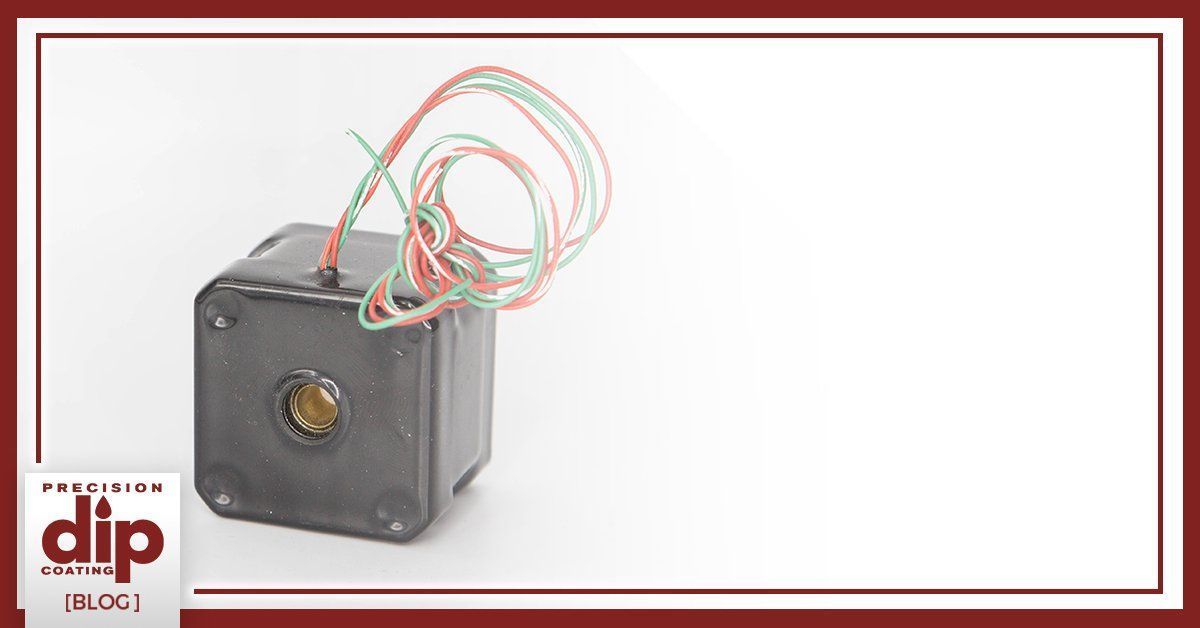
Determining Which Method Is Best for Your Products
Precision Dip Coating is a one-stop-shop Connecticut based company with over 20 years of industry experience providing the best coated and molded products on the market at a price you can afford. We are an in-house company who can provide you with everything from in-house engineering and development to production using our own custom designed coating machines, no matter what your product demands are.
Electrostatic Coating
Electrostatic coating is the process of painting with positively charged paint particles from a specialized gun to coat metal surfaces which have been grounded to create negatively charged metal surfaces. Working similarly to a magnet, the positively charged paint is drawn to the metal and coats it evenly and effectively with less than 5% waste whereas a standard method can waste as much as 20% to 60% to accomplish the same task. Once applied, the paint takes up to 24 hours to fully dry.
Advantages:
- Easier to coat difficult shapes
- Components do not need to be preheated
- Color changes are far simpler than with fluidized bed coating
- Low cost for automation
- Film thickness between 30-250 microns
Disadvantages:
- Equipment cost is far more expensive than with fluidized bed coating
Fluidized Bed Coating
This process of coating is a form of spray coating that occurs within a fluidized bed system. To achieve this method, items are placed inside a fluidized bed and moved around while simultaneously being sprayed with a liquid. This method results in an even distribution and provides a protective layer of coating, but does require a greater amount of powders and wasted material.
Advantages:
- Low initial cost to manufacture
- A high film thickness of >250 microns can be applied in one cycle and used as a protective layer
Disadvantages:
- Components must be simple in shape and not complex and thin gauge material cannot be coated with this method due to low-heat capacity.
- All pieces must be preheated in order to be worked with
- Color changes can only be accomplished through additional beds
- Film thickness of over 200 microns is average
We'll Help You!
With Precision Dip Coating you can be sure we will find the right style to meet your product's needs and demands at a price that fits your budget. So call Precision Dip Coating today to get started with industry professionals who can help you through every step of the design and production process.