Fluid Bed Powder Coating: Thermoplastic vs. Thermoset Powders
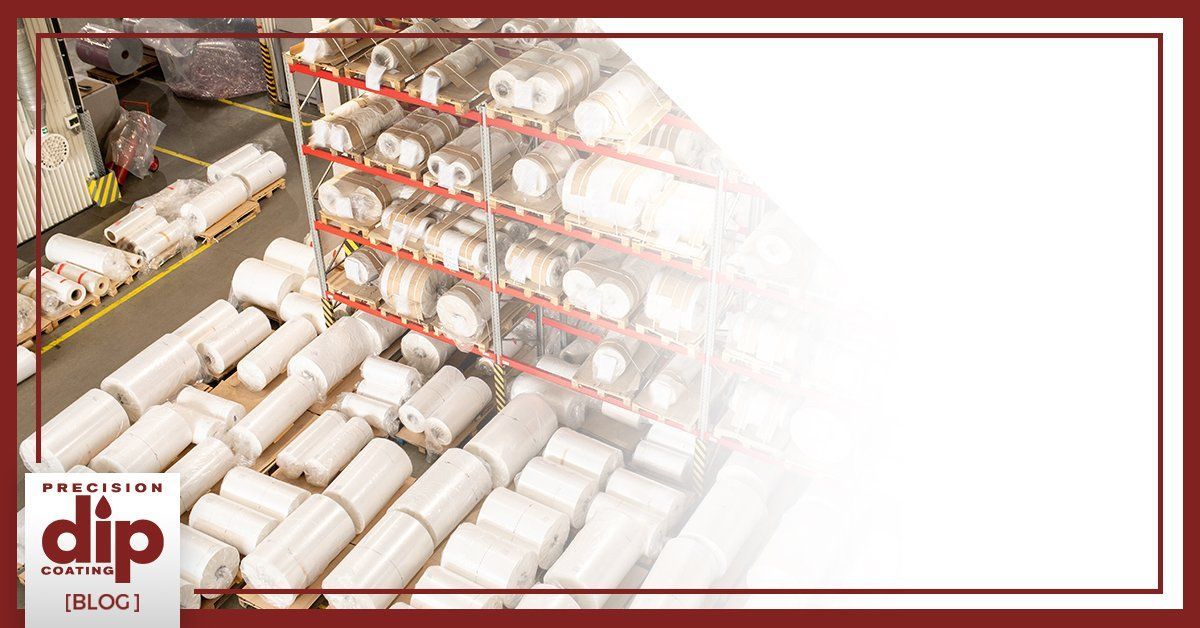
Powder coating can add attractive, durable protection to countless items used for everything from consumer goods and medical equipment to industrial parts and aerospace uses. Techniques for applying powder coatings, such as dip, spray, and fluid bed, and the type of material used can be chosen to provide the best match for the item to be coated and its intended use.
What Is Fluid Bed Powder Coating?
To apply a fluidized bed powder coating, a heated part is immersed in a bed of powdered plastic resin so that the plastic melts on contact, forming a film that's bonded to the piece. Typically, parts are heated after dipping to cure the plastic resin. Such coatings are similar to a dip coating, but are suited to a wider range of materials than typical dip coating materials offer. Fluidized bed coatings also tend to be a little thicker than with spray applications, and may be better at getting into some more challenging part geometries such as small wire grids.
Thermoplastic vs. Thermoset Powders
Thermoplastics and thermoset plastics achieve similar results but behave in critically different ways, making them suitable for different uses and environments. The primary difference between the two categories of materials is that thermoplastics can be remelted, recycled, and reused while thermoset plastics will remain strong and in their solidified form and cannot be remelted and reused or recycled in the same way. By far, the majority of fluidized bed coating applications involve thermoplastics which generally provide better, more consistent results. Typical plastics used with fluidized bed coating techniques include:
- Vinyl
- Epoxy
- Nylon
- Polyethylene
- Halar
At Precision Dip Coating, our decades of experience allow us to help you determine the most effective coating solutions to meet your specific needs.
Contact us today to learn more about our coating, molding, and value-added services.