Top 5 Reasons the Medical Industry Uses Plastic Dip Coating
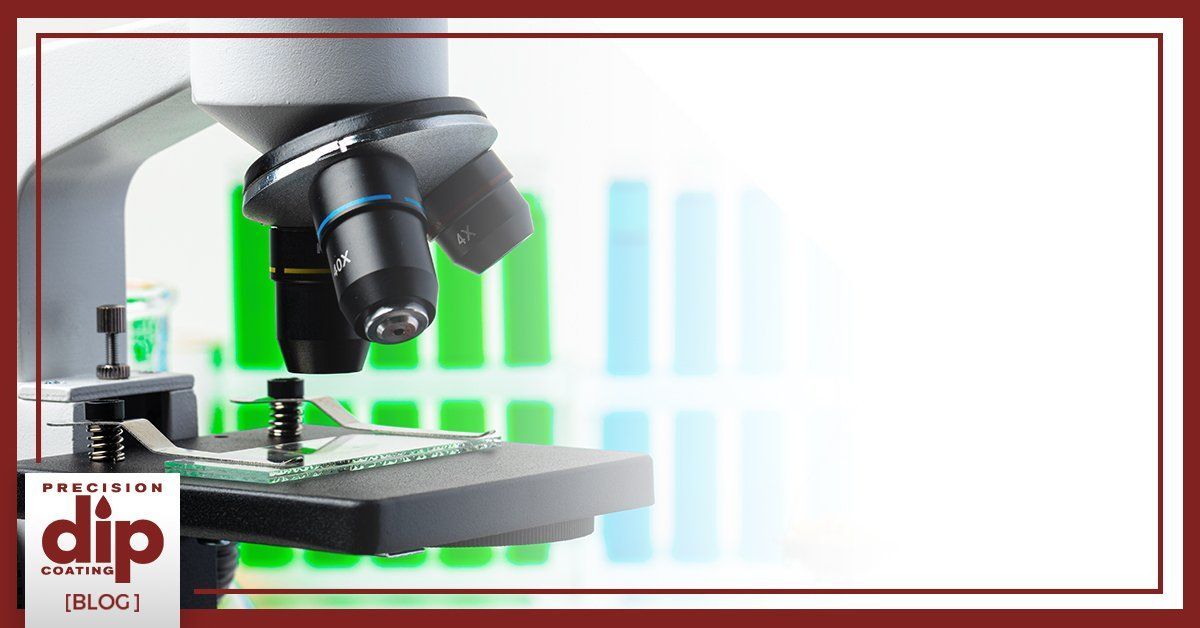
Plastic coatings can improve safety, protection, and durability among their many contributions to product quality and performance. Applied by spraying or dipping, these coatings find homes in numerous industries we serve, including the medical field.
What Is Dip Coating?
The dip coating process, as it sounds, involves pre-heating a part, dipping it in a customized vat of liquid plastic or fluidized powder, then heat curing it to solidify the plastic coating.
Reasons Plastic Dip Coating Is Used in the Medical Industry
Plastic coatings have, in many ways, revolutionized and improved many aspects of work in the medical industry. Five of the most important ways dip coatings contribute to the field of medicine are:
1. Dip Coating for Safety & Sterility
Plastic coatings can be impervious to moisture and many chemicals and other compounds, offering a safe, sterile surface for many pieces of medical equipment, such as tweezers, speculums, and sterilization case parts. Many coatings can also be antibacterial and antimicrobial, adding to their safety.
2. Dip Coating for Improved Grip
Coatings such as plastisol have a naturally rubbery feel, which can make equipment and handles coated with them easier to grip safely, even with wet hands. A plastisol dip coating can also make handles softer and more comfortable to grip, reducing hand fatigue.
3. Dip Coating for Durability
Because long-term performance is critical for medical equipment, the protective, resistant nature of dip coating can make parts last longer in the wide variety of environments encountered in the medical field.
4. Dip Coating for Improved Resistance
Coatings such as plastisol have a naturally rubbery feel, which can make equipment and handles coated with them easier to grip safely, even with wet hands. A plastisol dip coating can also make handles softer and more comfortable to grip, reducing hand fatigue.
5. Dip Coating for Better Performance
Some dip coatings offer superior smoothness, such as nylon, while others such as Halar create a minimal friction surface. These advantages can enhance performance, particularly with parts that need to work together closely.
At Precision Dip Coating, we have the knowledge and expertise to provide high-quality plastic coating services for the medical industry and dozens of others.
Contact us today to learn more about our full range of capabilities.