How Plastic Coating Is Done
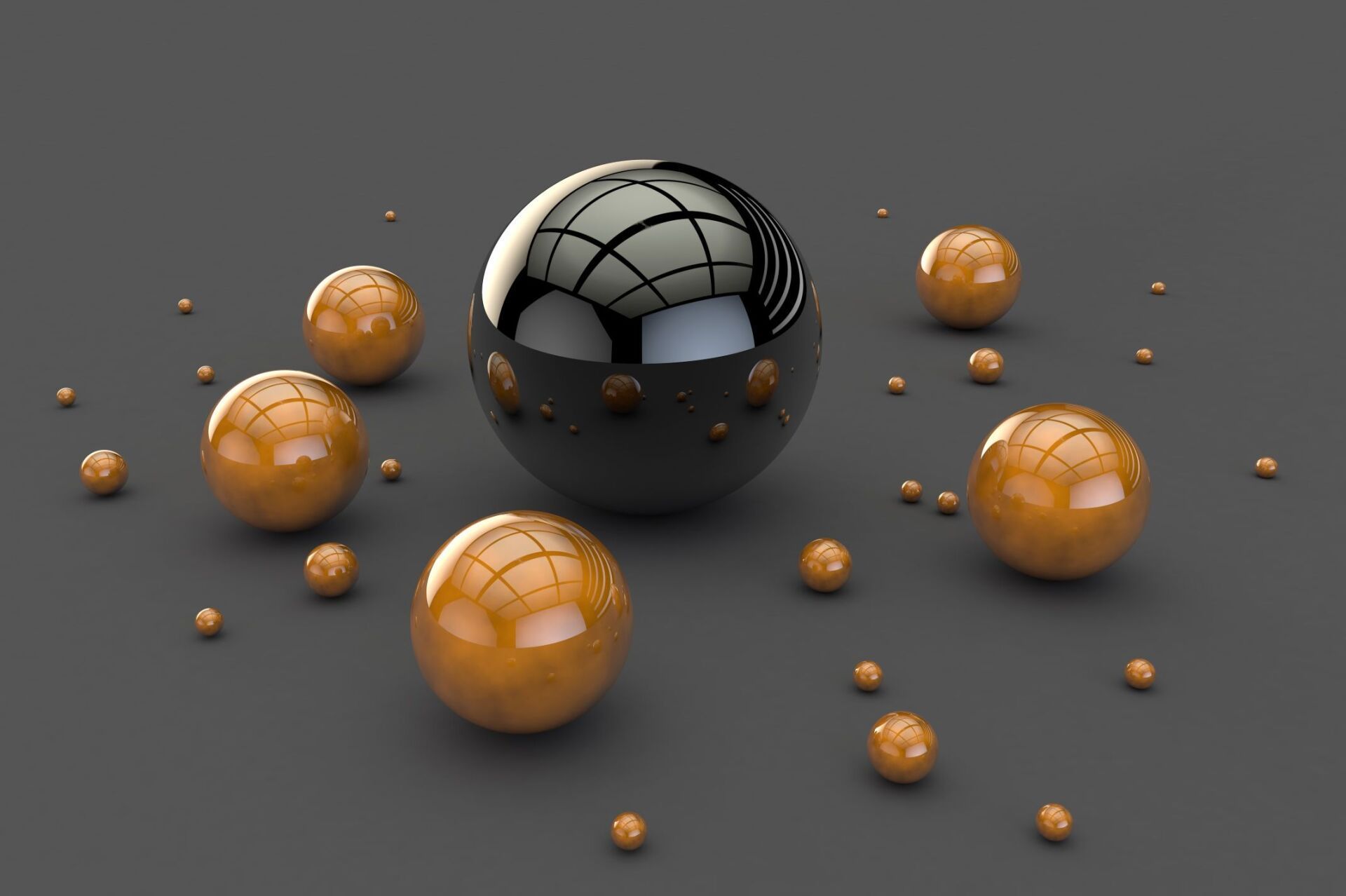
Plastic coating is an essential process that impacts countless aspects of our daily lives. From the protective handles on tools to corrosion-resistant car parts and insulated electrical components, plastic coatings provide safety, durability, and aesthetic appeal. But how is this versatile process performed, and why is it so critical? Let’s take a deep dive into the steps, techniques, and benefits of plastic coating.
What Is Plastic Coating and Why Is It Important?
Plastic coating involves applying a layer of liquefied plastic to an object, either by dipping, molding, or spraying. This process creates a protective barrier that enhances the object's functionality and longevity. The key benefits of plastic coating include:
Plastic coatings are widely used across industries such as automotive, medical equipment, electronics, and construction, making them indispensable in modern manufacturing.
Common Plastic Coating Techniques
Plastic coating can be achieved through several techniques, each suited to specific applications and material requirements. The most widely used methods include:
1. Hot Dip Coating
Hot dip coating is one of the most common plastic coating processes. It produces thick, durable coatings ranging from 1/16" to 1/4" in thickness. Steps in the hot dip coating process include:
2. Cold Dip Coating
Cold dip coating is similar to the hot dip method but does not involve preheating the object. This technique produces thinner coatings and is ideal for items that cannot withstand high temperatures. Steps in the cold dip coating process include:
3. Slush and Rotational Molding
For parts with hollow areas or complex geometries, slush and rotational molding are effective techniques. These methods allow plastisol to coat irregular surfaces evenly.
Types of Plastic Coating Materials
The choice of material is crucial to achieving the desired performance characteristics. Commonly used materials include:
Each material can be customized with additives to enhance properties like fire resistance, UV tolerance, and texture.
Applications of Plastic Coating
Plastic coating has countless applications across industries:
Advantages of Plastic Coating
Plastic coating is not just about aesthetics; it delivers a wide range of benefits that make it a preferred solution for manufacturers:
Why Choose Precision Dip Coating?
At Precision Dip Coating, we specialize in delivering high-quality plastic coating solutions tailored to your specific needs. Our expertise spans a range of techniques, including hot dip, cold dip, slush molding, and rotational molding. With decades of experience and ISO 9001:2015 certification, we guarantee results that exceed expectations.
In addition to plastic coating, we offer a full suite of value-added services, including:
Ready to Start Your Plastic Coating Project?
If you’re looking for affordable, durable, and visually stunning plastic coating solutions, contact Precision Dip Coating today. Let us help you enhance the performance and appearance of your products with our advanced coating techniques. Whether you need protection, durability, or aesthetic appeal, we have the expertise to make it happen!