Plastisol Coating Methods: Which Is Best for Your Project?
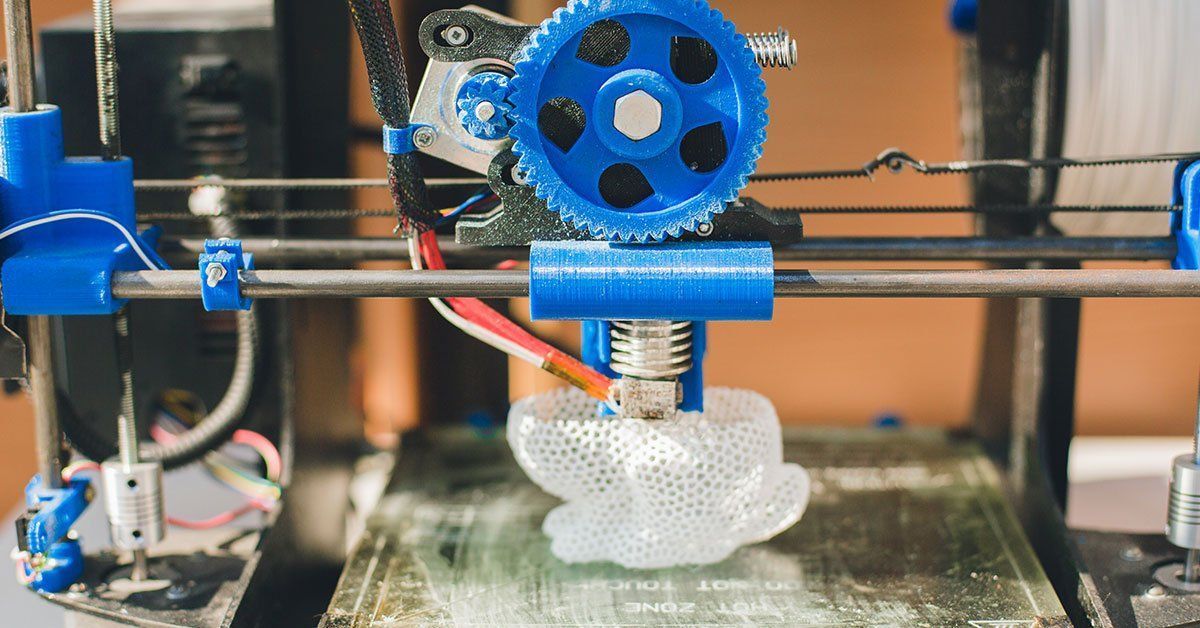
Cost-effective, highly durable, and very customizable, you'll probably find there's a plastisol coating to meet your needs. Part of plastisol's versatile appeal is that it lends itself well to multiple application methods, so you can select the approach that best meets your requirements.
What Is Plastisol?
Plastisol is, in its simplest form, a mixture of a thermoset plastic resin (usually polyvinyl chloride) and plasticizers which make it more rubbery and elastic. Durable and highly resistant, additives can enhance many of plastisol's characteristics including UV resistance, antimicrobial qualities, and flame retardance. Plastisol coatings can be tinted to nearly any color as well as having special finishes and appearances.
Plastisol Dip Coating
The most common technique for plastisol coatings, parts are partially or fully immersed in liquid plastisol, then heat cured. Parts may be preheated (hot dip) or not (cold dip) but some amount of heat curing is required to solidify the coating.
Best for:
Dip coating works with any items which can withstand the heat curing, and works best with those which can be preheated. Most dip coated items are metal, such as tool handles, wire baskets, and electrical components.
Plastisol Molding
With slush molding, parts are placed in a centrifuge and the spinning motion sends plastisol throughout the parts. In rotational molding, parts are turned while being coated so all areas are fully covered. Coated parts must be heat cured.
Best for:
Molding techniques work best for coating parts with hollows and concave areas or other crevices and cavities which might not be fully coated using other techniques.
At Precision Dip Coating, we have decades of expertise with plastisol and numerous other coatings.
Contact us today to learn more about our full range of dip and spray plastic coating capabilities.